Conformal coatings are necessary in certain applications to protect components on PCBs from physical impact and the corrosive effects of moisture in harsh environments which can lead to product failures.
If the conformal coating is not properly applied, the long-term reliability of a product can be compromised. For example, coating defects in the manufacturing process of electronic modules used in automobiles can threaten the safety & security of passengers. Even in today’s age of highly automated manufacturing processes, many companies still conduct inspection of the conformal coating manually. In such cases, depending on the degree of an operator’s proficiency and fatigue factors, human errors can occur. Reducing such human errors and improving the quality and the repeatability of the inspection process is the role of an automated conformal coating inspection machine.
The key point in conformal coating defect detection is the degree of illumination of the coating. This is accomplished by adding a tracer material into the coating which will cause it to illuminate when exposed to a UV light source. PARMI’s PCI 100’s illuminating system (1) obtains the inspection image through UV LED lighting for conformal coating and bubble inspection and (2) utilizes white LED lighting for teaching and fiducial mark recognition. PARMI utilizes a very innovative simultaneous image acquiring technique in a single scan from both UV LED and White LED, so the inspection time is very fast. After scanning a sample coated PCB, by simply clicking the Magic Wand button, the programmer is able to define the coated and non-coated (keep out) areas on the PCB. PARMI’s PCI 100 can inspect coated PCB’s for the following attributes: Coating presence, coating absence (keep out), overspray / contamination, bubbles and optionally measure coating thickness in defined locations.
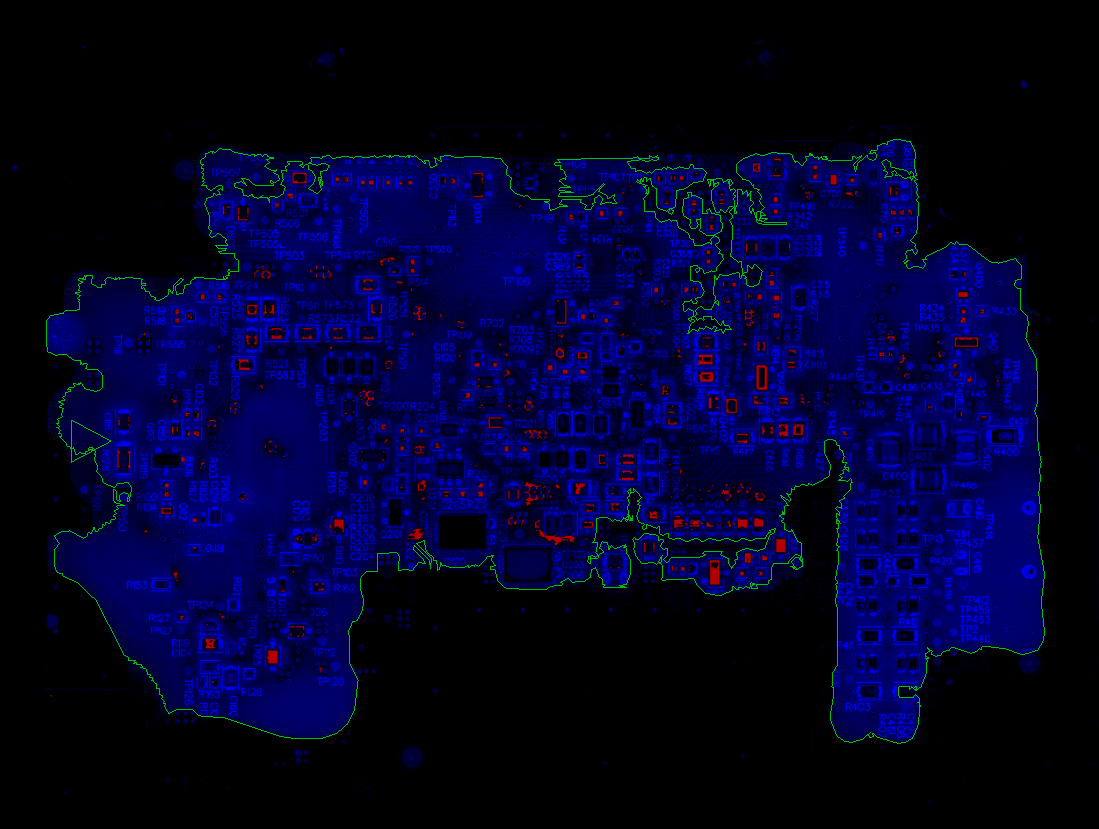
As mobile devices and wearable devices become smaller and thinner, coating thickness must be strictly controlled. The coating must be thick enough in order to protect components, and thin enough to have competitiveness in portability and to minimize the consumption of the coating materials. In order to meet the standards of coating thickness, PARMI’s CTS I (Coating Thickness Sensor) can be optionally added to the PCI 100 machine. Measurement reliability of the thickness sensor is improved by first finding the measurement target height on the PCB with a laser module in the PCI 100’s sensor head, and then secondly adjusting the Z-axis to the precise focal distance prior to making the thickness measurement of the coating.
PARMI’s PCI 100 DSI (Double Side Inspection) can inspect the top and bottom sides of a PCB in one continuous operation, by flipping the PCB inside the machine. It maximizes production efficiency with a shorter cycle time by minimizing unnecessary processes and minimizes floor space required by eliminating the need for an external board flipper.
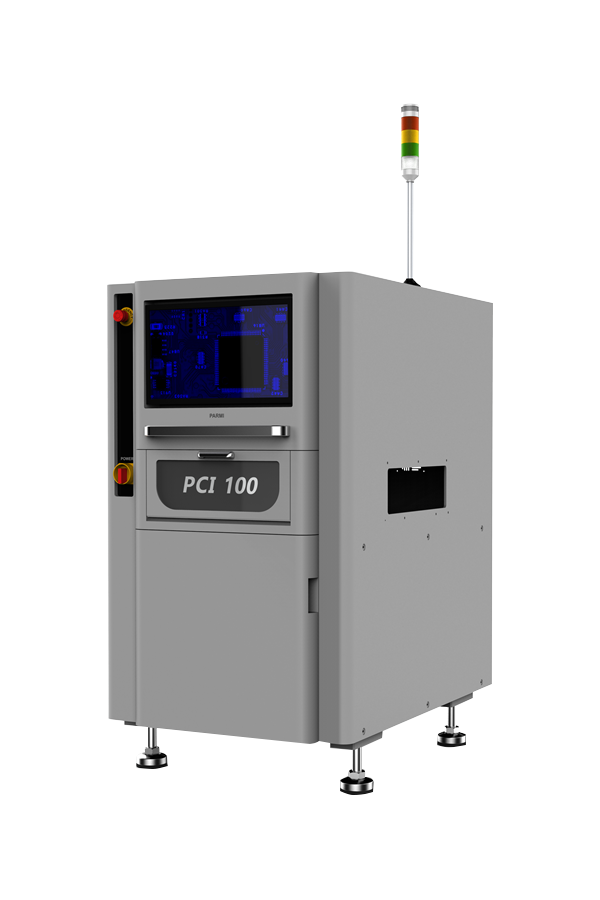
For more information on Parmi please visit the website at www.Parmi.com