Yamaha Robotics SMT Section has introduced three hardware-based performance options for high-speed mounters that enhance productivity, quality control, and flexibility for handling special products such as large LED boards. Available for all new Yamaha mounters, these options are designed for easy fitting to simplify upgrading equipment already in the field.
The new features include nozzle-tip force measurement for early detection of issues such as blockages. Accurately tracking any changes in force allows timely nozzle maintenance, such as cleaning, to ensure optimal end-of-line production yield. Implemented with a module fitted at the mounter’s feeder interface, the system provides an easy menu-driven setup and measures the component-placement force to within 0.1N resolution. The nozzle tip force measurement option is available now and compatible with Yamaha YRM mounters.
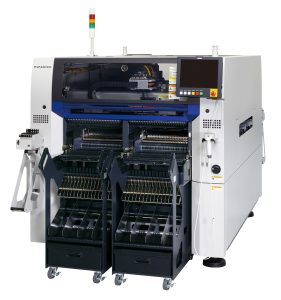
Also new, LCR verification measures the inductance, capacitance, or resistance value of components in SMD-chip packages to verify the correct part type and tolerance before placement. This lets users instantly detect issues such as feeder errors, reel errors, or defective components before placement, to maximise first-pass yield and avoid rework. The LCR unit can be fitted to Yamaha YRM mounters and legacy YSM machines, with no special software or hardware modifications required. LCR verification and nozzle-tip force measurement are ideal for markets with high quality-management demands, such as automotive, aerospace, and medical.
Finally, the large board option lets YRM mounters handle boards up to 1.5 metres long and 510mm wide, for populating challenging assemblies such as extra-large LED-lighting boards. While increasing the maximum board size by more than 30% compared to the standard YRM mounters, the new option accepts boards up to 10mm thick and weighing up to 10kg. These extended capabilities let product manufacturers easily work with assemblies designed for high thermal capacity, such as heavy-gauge copper or aluminium insulated metal substrate (IMS).
The new options can be implemented individually or together to boost surface-mount production performance and extend the advantages of the 1 STOP SMART SOLUTION, which comprises Yamaha’s YRP printers, YRM-D dispensers, YRM mounters, and YRi-V inspection systems. The 1-STOP SMART SOLUTION lets users configure a complete SMT assembly line from Yamaha, unified with a common software platform and smart tools that ensure superior flexibility, quality, and productivity.
About Yamaha Robotics SMT Section
Yamaha Surface Mount Technology (SMT) Section, a subdivision of Yamaha Motor Robotics Business Unit in Yamaha Motor Corporation, produces a complete selection of equipment for high-speed inline electronic assembly. This 1 STOP SMART SOLUTION includes solder paste printers, component mounters, 3D solder paste inspection machines, 3D PCB inspection machines, flip-chip hybrid placers, dispensers, and management software.
Bringing the Yamaha way to electronics manufacturing, these systems prioritize intuitive operator interaction, efficient coordination between all inline processes, and modularity enabling users to meet the latest manufacturing demands. Group competencies in servo-motor control and image recognition for vision (camera) systems ensure extreme accuracy with high speed.
The current product line includes the latest YR equipment generation, with advanced automated features for programming, setup, and changeovers, and new YSUP management software with state-of-the-art graphics and built-in data analytics.
Combining design and engineering, manufacture, sales, and service competencies, Yamaha SMT Section ensures operational efficiency and easy access to support for customers and partners. With regional offices in Japan, China, Southeast Asia, Europe and North America, the company provides truly global presence.