Empowering component mounters to monitor their own performance and detect anomalies in real time allows production to handle faults and unexpected events. By preventing minor issues from escalating into costly downtime, production can continue without halting and engineers can diagnose and fix any underlying problems at a suitable time. This can help reduce operational disruptions and improve overall equipment effectiveness (OEE), ultimately leading to greater productivity.
Enhanced Adaptability
Both software- and hardware-based systems have their place in ensuring manufacturing equipment can autonomously adapt to issues, securing continuous production and high productivity. In equipment such as high-speed surface mounters that contain inspection cameras and motion controls already built-in, these can provide a convenient opportunity to add new self-test capabilities by applying a software update. On the other hand, new hardware may be needed to introduce new tests that require extra sensors or actuators.
Nozzle problems, often due to blockages, are a common issue that surface-mount production teams must deal with frequently. Nozzles are loaded and unloaded from the placement head and kept in a storage station when unused. The position of each nozzle is assigned at setup and typically remains fixed until the machine is reprogrammed at the next product changeover.
In Yamaha’s latest YRM mounters, new Nozzles-Free Layout software (figure 1) lets the machine manage the nozzles according to their identity and not by their positions in the nozzle station. Each nozzle has a unique identity assigned with a 2D code. With nozzles-free layout, the machine returns nozzles to any station position.
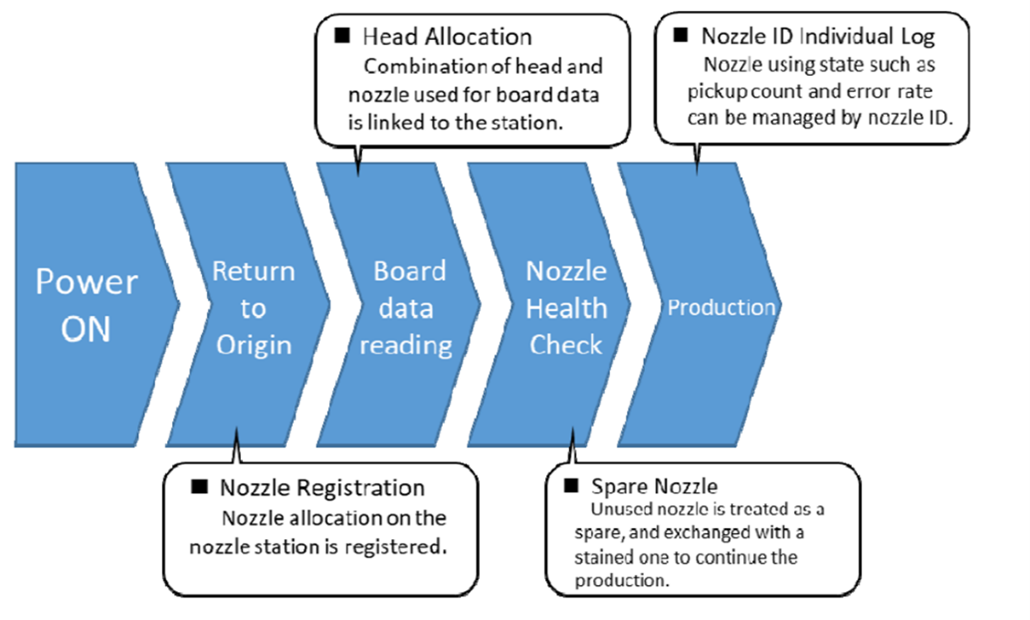
Applying this software allows the machine to avoid problems with a poorly performing nozzle by taking another of the same type from a different position. Production continues without interruption so the faulty nozzle can be examined to remedy the defect. The nozzles-free layout option helps to minimise operator errors after cleaning or maintenance and lets production teams accurately monitor nozzle performance.
This example shows how a software change can enhance fault-tolerant operation. On the other hand, a new nozzle tip force measurement option for spring-loaded nozzles requires new hardware to be installed. Adding this feature lets the mounter check periodically for nozzle issues. The new hardware contains a load-cell assembly that works with accompanying software for controlling the nozzle-testing sequence (figure 2).
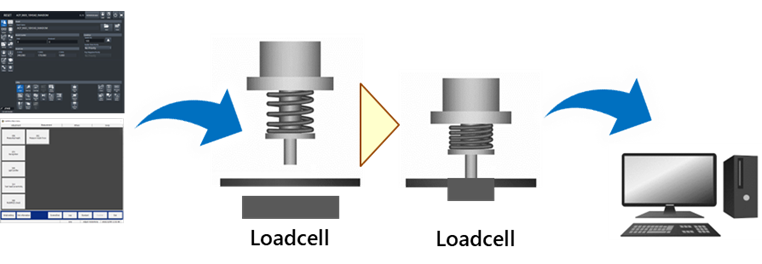
The upgrade is fitted on the mounter’s feeder bar and can be installed during build-up of a new machine or retrofitted to existing machines while in situ on the factory floor. The measurements confirm whether the nozzle tip force is within the usual range, typically between 0.5-0.8 Newton. Abnormal force indicates an issue such as blocking, which can happen when debris interferes with spring operation. By measuring the component-placement force to within 0.1N resolution, this system provides an early warning before spring problems cause assembly defects. The tip force measurement results also aid troubleshooting, allowing the cause of the defect to be traced and fixed quickly. The associated software assists with calibration as soon as the load cell is fitted and presents menu-driven instructions to guide the operator through the measurement procedure during normal operation.
Easy to Add Hardware
Alternatively, the LCR Unit, specific to Yamaha mounters, provides an example of a hardware-based upgrade that can be introduced with no modifications to the mounter. Effectively containing a digital multimeter built into a standard feeder-size format, this unit is designed to be extremely easy to install. After a component is picked, the multimeter measures the value before the part is on the board. It is capable of measuring inductive, capacitive and resistive components and can be used at specific times, such as immediately after a reel is replaced. Checking component values with this unit confirms that the new reel contains parts of the same value and tolerance as shown on the label. Defective components are rejected immediately (figure 3).
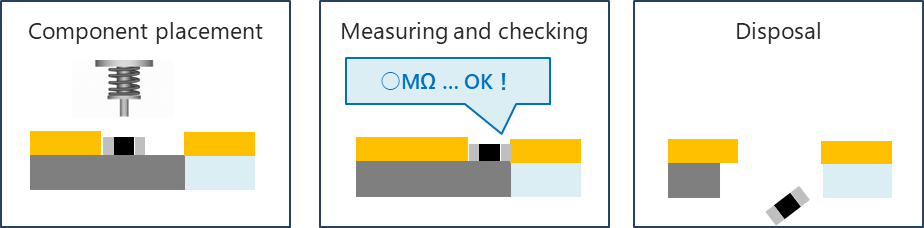
Figure 3. The LCR Unit is easy to fit and measures component values automatically.
A mounter equipped with the LCR Unit can instantly detect issues such as feeder errors, reel errors, or defective components before placement. This helps maximise first-pass yield and avoid rework. The unit occupies two standard 8mm feeder positions and can be fitted to any of Yamaha’s mounters in a live factory environment, as easily as changing a feeder. No special software is required and there is no need to halt production. LCR checking enhances quality assurance and is particularly valuable when low-cost components are used, or to enhance traceability in automotive, medical, or aerospace industries.
Non-Stop Productivity
There are additional software-only upgrades for Yamaha mounters, including automatic multi-vendor component support and on-the-fly component pickup evaluation. The multi-vendor function helps operators avoid any problems that may arise if the company’s purchasers source one component type from several different suppliers. The components as supplied may be oriented differently in tape pockets, the tape-feeder pitch may be different, or there may be other visible differences. These could cause the machine to perceive a component error and unnecessarily interrupt production. By applying the Automatic Multi-Vendor Support software upgrade, the component database can adapt to such differences so that production can continue.
Pickup evaluation uses the mounter’s side-view camera, fitted as a standard feature, to check the component orientation after picking. It provides a quick way to test the stability of important mounter parameters like the pickup height, X-Y movement, and vision recognition. This option generates optimised pickup data that helps to minimise the setup time per component during new product introduction, as well as helping optimise component information during production. By enabling automated settings and judgements, this software can help quickly determine nozzle compatibility, optimise placement-head excursion speed, and judge pickup information, cutting the decision-making time to just a few seconds.
In addition, auto-teaching extends the capabilities of offline editing software to allow fine-tuning of library and gerber data and help determine any corrections that should be applied before production begins. This lets production teams avoid building test boards to check correct component alignment and orientation. An additional and powerful software tool provides automated assistance for removing unused parts feeders. Production teams commonly face challenges at product changeover if the new product requires extra component feeders although the mounter’s feeder positions are already full. Identifying unused feeders by manual inspection can be difficult, requiring time-consuming cross-referencing between programs. Yamaha’s unused parts feeder removal software has automated this analysis and quickly identifies feeders that can be changed, helping quickly complete the changeover and restart production to maintain productivity.
Another upgrade, now available, introduces a large-board option by fitting an enhanced conveyor (figure 4) strong enough for boards up to 10kg in weight and up to 10mm thick. Compatible with single-beam YRM20 mounters, the conveyor handles boards up to 1.5 metres long and is ideal for products such as extra-large LED-lighting assemblies built with heavy-gauge copper or aluminium insulated metal substrate (IMS).
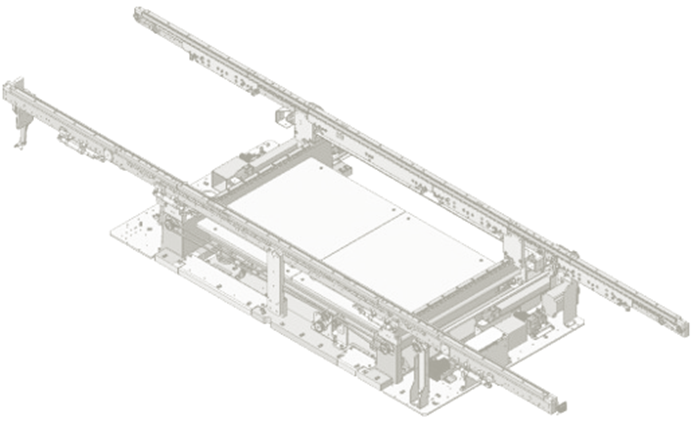
Conclusion
Optional hardware and software upgrades can be applied to SMT assembly equipment, giving the ability to anticipate, detect, diagnose, and respond to issues autonomously. Adding intelligence and resilience in this way can help to prevent stoppages caused by small problems that can be easily avoided or fixed, raising productivity and freeing operators to focus their attention on issues that need the human touch.
To learn more, visit www.smt.yamaha-motor-robotics.de or www.yamaha-motor-robotics.eu