TANAKA Kikinzoku Kogyo K.K. (Head office: Chiyoda-ku, Tokyo; Group CEO: Koichiro Tanaka), which develops industrial precious metals products as one of the core companies of TANAKA Precious Metals, announced that it has established a jig cleaning method called TANAKA Green Shield. This cleaning method is characterized by nickel plating on the adhesion-preventing plate1, a component of vacuum film formation equipment2 used in semiconductor manufacturing and other processes. When using a nickel-plated adhesion-preventing plate, PGM3 sputtered films, including platinum and palladium, can be easily detached from the plate.
TANAKA is developing a recycling business for this use case. After detaching sputtered films adhering to components, mainly made from stainless steel, of vacuum film formation equipment such as sputtering and vacuum deposition equipment, the recovered precious metals are refined and returned to the customer with the precision-cleaned components.
This cleaning method takes advantage of a unique TANAKA technology related to base plating. Applying a nickel plating to an adhesion-preventing plate enables PGM sputtered films to be detached through chemical treatment without damaging the base material. This method makes it easier than previous methods to detach PGM sputtered films, so it is expected to reduce the amount of cleaning agent required when cleaning equipment, in turn contributing to reduced environmental impact. With an anticipated reduction in recovery loss of precious metals scattered around during the grinding process, this method is also expected to achieve higher PGM recovery rates with lower costs.
TANAKA aims to develop the TANAKA Green Shield system to support a wide variety of component shapes and sizes and to expand PGM film recovery rates by six times the current level by 2025.
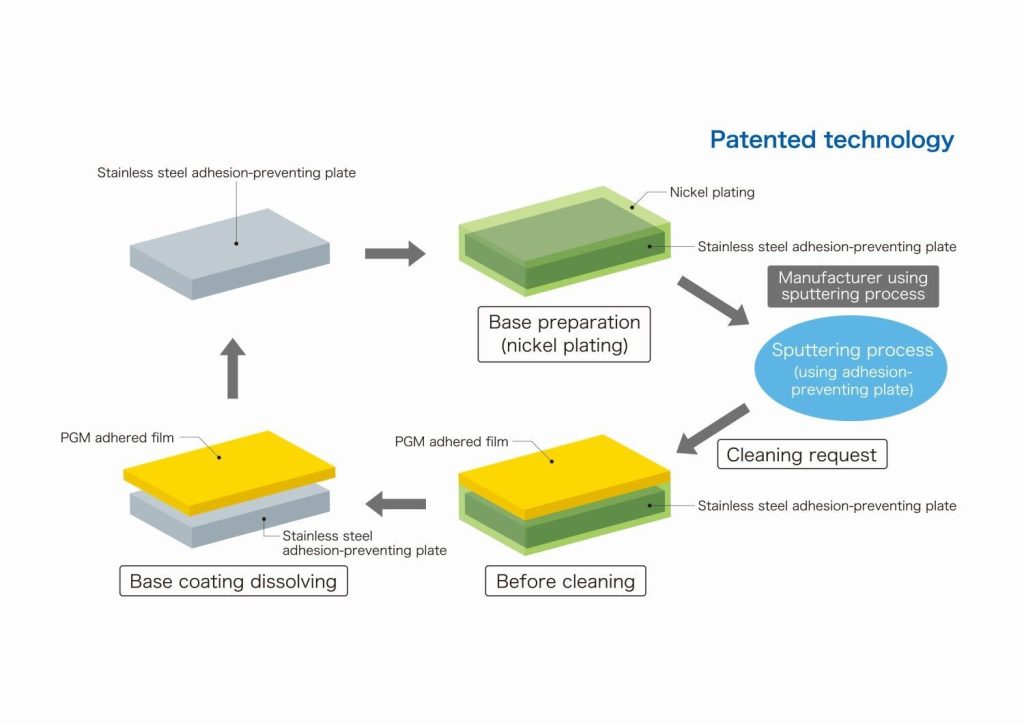
Jig Cleaning Method
There are multiple jig cleaning methods for vacuum film formation equipment components, including physical detachment (blast cleaning) and thermal sprayed aluminum base film formation. Physical detachment, in which an abrasive agent (cleaning agent) is sprayed to remove an adhered film, is currently a commonly used jig cleaning method due to its low cost. Use of an abrasive agent damages the surface of the base material, thereby leading to reduced lifetime of the base material. Another disadvantage of this method is that material is scattered during the process, causing a loss in precious metal recovery.
Another method for detaching an adhered film is the thermal sprayed aluminum base film formation method of jig cleaning. This requires the adhesion-preventing plate to be coated with aluminum in advance using a thermal spraying method, and the aluminum to be then dissolved with chemicals. Drawbacks of this approach include challenges in recovering adhered film from surfaces lacking an aluminum coating, as well as the elevated cost associated with forming the aluminum film.
TANAKA Green Shield is a base preparation method whereby nickel plating is applied to an adhesion-preventing plate prior to use. After using a plate in a sputtering process, for example, only the nickel plate coating between the adhesion-preventing plate and PGM sputtered film is dissolved. This enables not only the PGM sputtered film but also other adhered films with various compositions to be detached from the plate without damaging the base material. This base preparation has a high level of adhesion with adhesion-preventing plates and sputtered films, which can prevent sputtering defects caused by peeling of sputtered film. A wide variety of component shapes can also be nickel-plated with this method. In addition to preventing degradation of the base material, this cleaning method is cheaper than the aluminum film formation method. It also requires lower amounts of cleaning agent, making it an environmentally friendly, next-generation jig cleaning method.
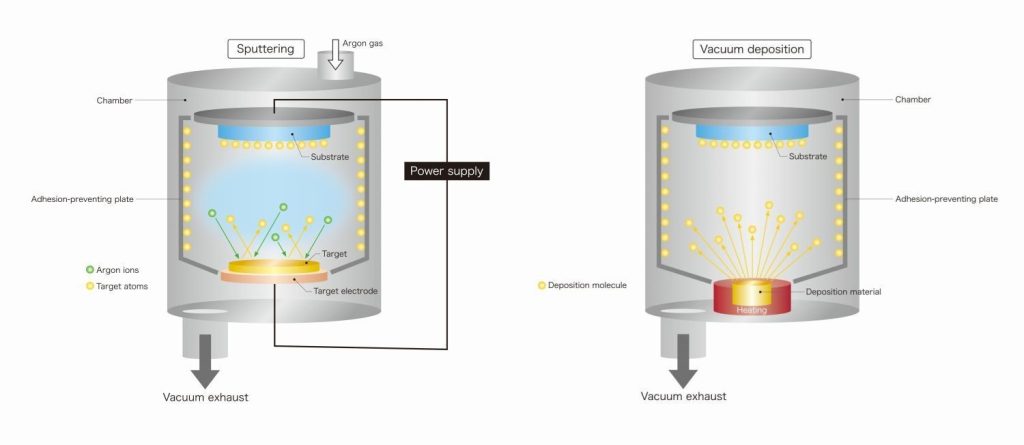
TANAKA and the Circular Economy
Since it was founded in 1885, TANAKA has continuously operated a precious metals recycling business. In addition to its existing precious metals recycling technologies, developed through research into precious metals over these many years, the company is now developing the TANAKA Green Shield, with a range of new precious metals recycling technologies. TANAKA’s precious metals recycling business promotes the recycling of limited precious metal resources and contributes to the realization of a circular economy.
[1] Adhesion-preventing plate: Plate installed to prevent film adhering to the interior wall of a film formation chamber (sealed reaction vessel used for producing physical or chemical reactions)
[2] Vacuum film formation equipment: Equipment used in thin film formation processes, including sputtering and deposition, employed in the manufacture of semiconductors
[3] PGM: Platinum group metals comprising six precious metals (platinum, palladium, rhodium, ruthenium, iridium, and osmium)
About TANAKA Precious Metals
Since its foundation in 1885, TANAKA Precious Metals has built a portfolio of products to support a diversified range of business uses focused on precious metals. TANAKA is a leader in Japan regarding the volumes of precious metals handled. Over the course of many years, TANAKA has not only manufactured and sold precious metal products for industry but also provided precious metals in such forms as jewelry and assets. As precious metals specialists, all Group companies in Japan and around the world collaborate and cooperate on manufacturing, sales, and technology development to offer a full range of products and services. With 5,355 employees, the group’s consolidated net sales for the fiscal year ending March 31, 2023, was 680 billion yen.
Global industrial business website
www.tanaka-preciousmetals.com
Product inquiries
TANAKA Kikinzoku Kogyo K.K.
www.tanaka-preciousmetals.com/en/inquiries-on-industrial-products/