Yamaha Robotics SMT Section has released new YSUP smart factory software with automatic troubleshooting, and previewed the advanced functionality to Productronica visitors during the Munich event’s technical program in November.
Presenting at the Productronica Forum, Yamaha’s Kamil Stasiak, SMT Section product marketing manager, described in-depth the new YSUP Analytics Dashboard that quickly identifies the causes of any assembly defects. The new functionality increases production efficiency and enables every shift to achieve consistent productivity by relieving reliance on the production team’s diagnostic skills.
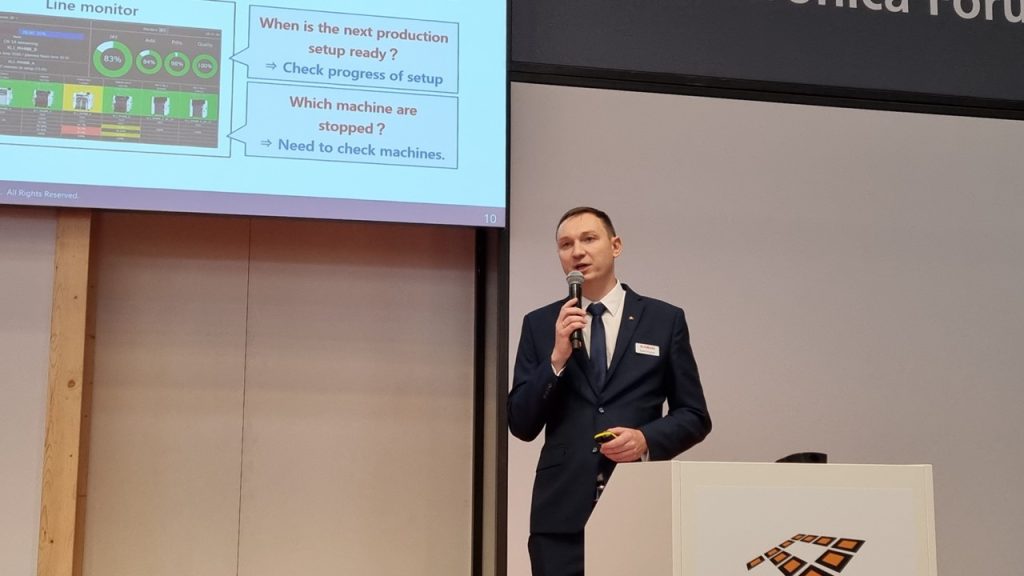
Operating continuously while assembly is ongoing, the auto-analytical functionality works with data from inline inspection systems and generates clear instructions for operators to take remedial action. The system also displays the effects of improvements on the YSUP Dashboard monitor to keep production teams always up to speed with progress. The underlying platform is based on statistical techniques and allows scaling to add further analytics tools.
The Forum audience learned how the software identifies probable causes of recorded exceptions in near real-time using analytical methods including flow judgement, error-code diagnostics, health-check data diagnostics, and image-recognition diagnostics. Its capabilities include automatic pickup error analysis, which lets production staff view the time and circumstances of any pickup errors, see the exact location, and view corrective actions.
The new Dashboard is fully integrated in Yamaha’s YSUP intelligent factory software, which provides production support tools for planning, implementing, measuring, and improving manufacturing on surface-mount production lines. The tools include applications for scheduling production, creating work orders, programming inline equipment, managing components, monitoring production status, ensuring traceability, predicting results, and reviewing workflows.
Among several new features added in recent software releases, YSUP-MI enhances management of materials on assembly lines and YSUP-LINK connects production equipment with enterprise systems using industry-standard protocols. Also, YSUP-OC operation control generates work instructions, handles warnings and error notifications, and helps operators sort and prioritise their tasks.
The unifying GUI ensures intuitive operation with easy access to settings and production status information expressed in clear charts and graphics. The YSUP Dashboard, now with auto analytics as explained in depth at the Productronica Forum, also features pickup analysis, accuracy analysis, print analysis, and real-time production monitoring.
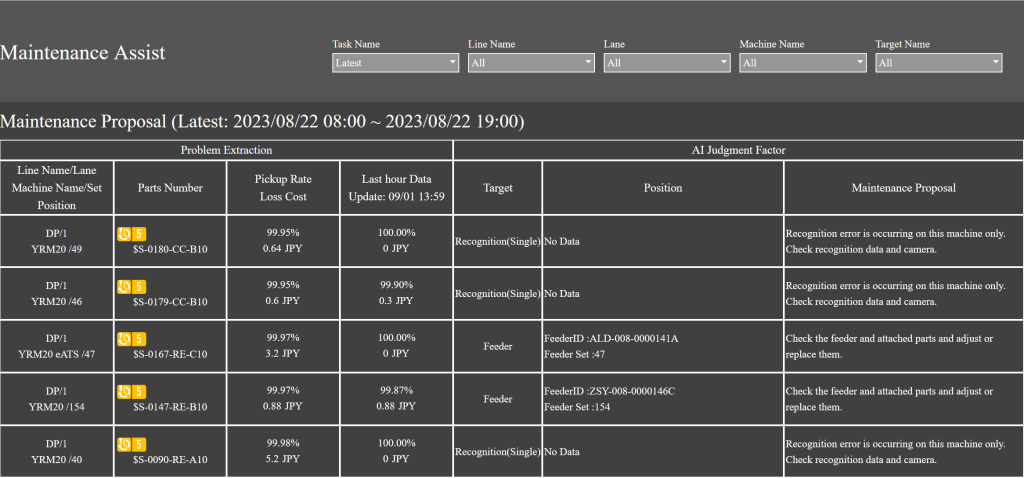
About Yamaha Robotics SMT Section
Yamaha Surface Mount Technology (SMT) Section, a subdivision of Yamaha Motor Robotics Business Unit in Yamaha Motor Corporation, produces a complete selection of equipment for high-speed inline electronic assembly. This 1 STOP SMART SOLUTION includes solder paste printers, component mounters, 3D solder paste inspection machines, 3D PCB inspection machines, flip-chip hybrid placers, dispensers, intelligent component storage, and management software.
Bringing the Yamaha way to electronics manufacturing, these systems prioritize intuitive operator interaction, efficient coordination between all inline processes, and modularity enabling users to meet the latest manufacturing demands. Group competencies in servo-motor control and image recognition for vision (camera) systems ensure extreme accuracy with high speed.
The current product line includes the latest YR equipment generation, with advanced automated features for programming, setup, and changeovers, and new YSUP management software with state-of-the-art graphics and built-in data analytics.
Combining design and engineering, manufacture, sales, and service competencies, Yamaha SMT Section ensures operational efficiency and easy access to support for customers and partners. With regional offices in Japan, China, Southeast Asia, Europe and North America, the company provides truly global presence.