Can electronics manufacturing be reconfigured for our digital, environmentally-conscious age? IDTechEx’s new report, “Manufacturing Printed Electronics 2023-2033”, explores a wide range of manufacturing innovations that will enable additive, digital, and higher throughput electronics production across many length scales.
Drawing on interviews and interactions with over 40 companies, this IDTechEx report analyzes developments, transitions, and technological innovations within printed electronics manufacturing. It assesses the attributes, readiness level, use cases, players, and market demand across many types of analog and digital printing, along with the motivation, challenges, and facilitating technologies associated with the transition toward continuous manufacturing.
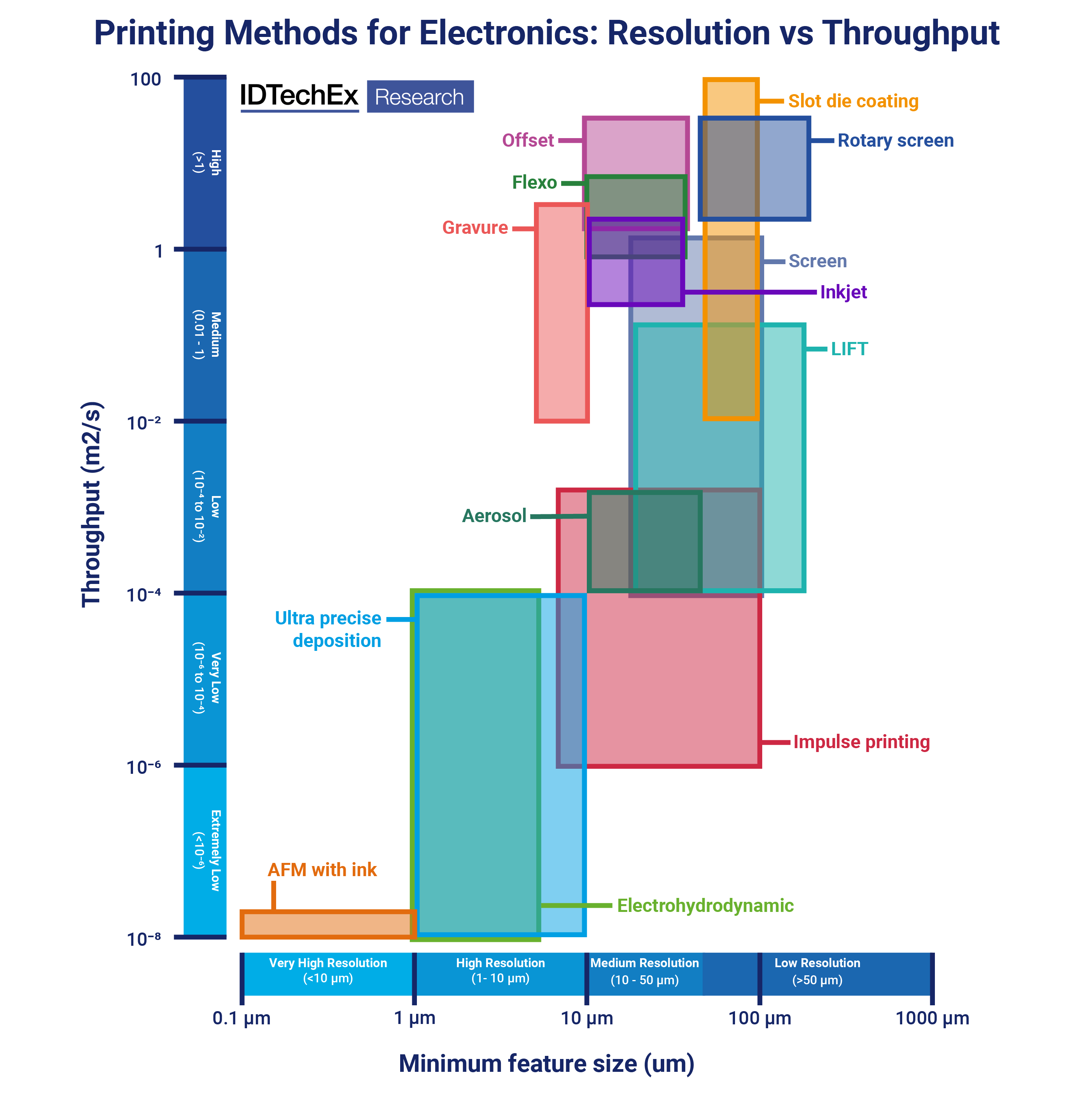
Transition to R2R Manufacturing
Compatibility with rapid roll-to-roll (R2R) manufacturing is commonly cited as a key value proposition of printed/fixed electronics. Utilizing methods from conventional graphics printing, R2R manufacturing will enable cost-sensitive large-volume applications such as smart packaging and electronic skin patches. Furthermore, the high throughput of R2R electronics is ideally suited for producing large-area devices such as photovoltaic panels, lighting, and outdoor displays.
However, thus far, most R2R electronics manufacturing (RFID excepted) has largely remained confined to research centers and pilot lines. Some of the challenges associated with adopting R2R electronics manufacturing include establishing sufficient order volume, quality control, and component attachment. The report explores these issues and outlines emerging technological solutions such as high throughput digital printing, contactless in-line conductivity measurement, and photonic soldering.
Digital Printing Methods
While R2R manufacturing typically utilizes conventional analog graphics printing methods (such as flexography), much of the innovation is within digital deposition methods that enable rapid prototyping and facilitate high mix low volume manufacturing (HMLV). Especially notable is laser-induced forward transfer (LIFT), which can be regarded as combining the benefits of inkjet, screen printing and direct laser structuring. This digital method can handle viscous inks, has a high throughput (being optically driven), and can even be used on non-planar surfaces since it’s a non-contact method.
Other emerging printing methods aim to bring additive digital manufacturing to length scales currently achieved with subtractive methods. Electrohydrodynamic (EHD) printing, in which traces as narrow as 1 um are produced using an electric field, is gradually gaining commercial traction for prototyping and repairs. Furthermore, multiple companies are developing multi-nozzle systems using MEMS (micro electromechanical systems) printheads to somewhat break the longstanding trade-off between throughput and viscosity.
Key Questions Answered in the IDTechEx Report:
- What are the options for manufacturing printed/flexible electronics across different length scales and throughputs?
- What are the advantages of additive over subtractive manufacturing?
- What are the emerging manufacturing technologies for printed/flexible electronics, and what is their technological and commercial readiness status?
- What are the challenges associated with adopting R2R electronics manufacturing? How can these be resolved?
- Which manufacturing technologies are best suited to each application?
- Who are the key players producing each manufacturing technology? How do they compare?
- What are the innovations in component placement and attachment that facilitate flexible hybrid electronics?
Outlook
It is an exciting time for printed/flexible electronics, with multiple examples reaching commercial adoption over the last year. The manufacturing innovations outlined in this report will bring roll-to-roll, additive and digital electronics manufacturing to applications ranging from electronic skin patches to advanced semiconductor packaging.
IDTechEx has 20 years of expertise covering printed and flexible electronics, including printing and manufacturing methods. Our analysts have closely followed the latest developments in the technology and associated markets by interviewing many equipment suppliers and product developers, along with annually attending multiple printed electronics conferences such as LOPEC and FLEX. “Manufacturing Printed Electronics 2023-2033” provides a comprehensive picture of the manufacturing landscape for this emerging technology, helping to support choices in product development and when scaling up to mass production.
To find out more about this new IDTechEx report, including downloadable sample pages, please visit www.IDTechEx.com/ManufacturingPE.
About IDTechEx
IDTechEx guides your strategic business decisions through its Research, Subscription and Consultancy products, helping you profit from emerging technologies. For more information, contact research@IDTechEx.com or visit www.IDTechEx.com.