Viscom AG continues its success story in the field of manual and automated X-ray inspection (3D-MXI) with a new high-quality system: like its predecessor X8011-II PCB, the X8011-III offers outstanding flexibility in inspection tasks and extremely high resolutions – plus brilliant and highly detailed image quality.
The design of the X8011-III with the large, white luminous “V” deliberately resembles the exterior appearance of the iX7059 systems developed by Viscom for the most exacting demands in inline X-ray inspection (3D-AXI). As such, the completely redesigned housing reflects features known to be a real advantage of Viscom’s manual X-ray systems. Just like the inspection gates in the production line, they can independently perform fully automatic quality inspections. Extensive analysis functions and intuitive operation enable fast, easy and precise inspection – while providing system users with key information on product quality. Today, 3D-AXI and 3D-MXI from Viscom are more “in tandem” than ever before – especially when it comes to the automatic software.
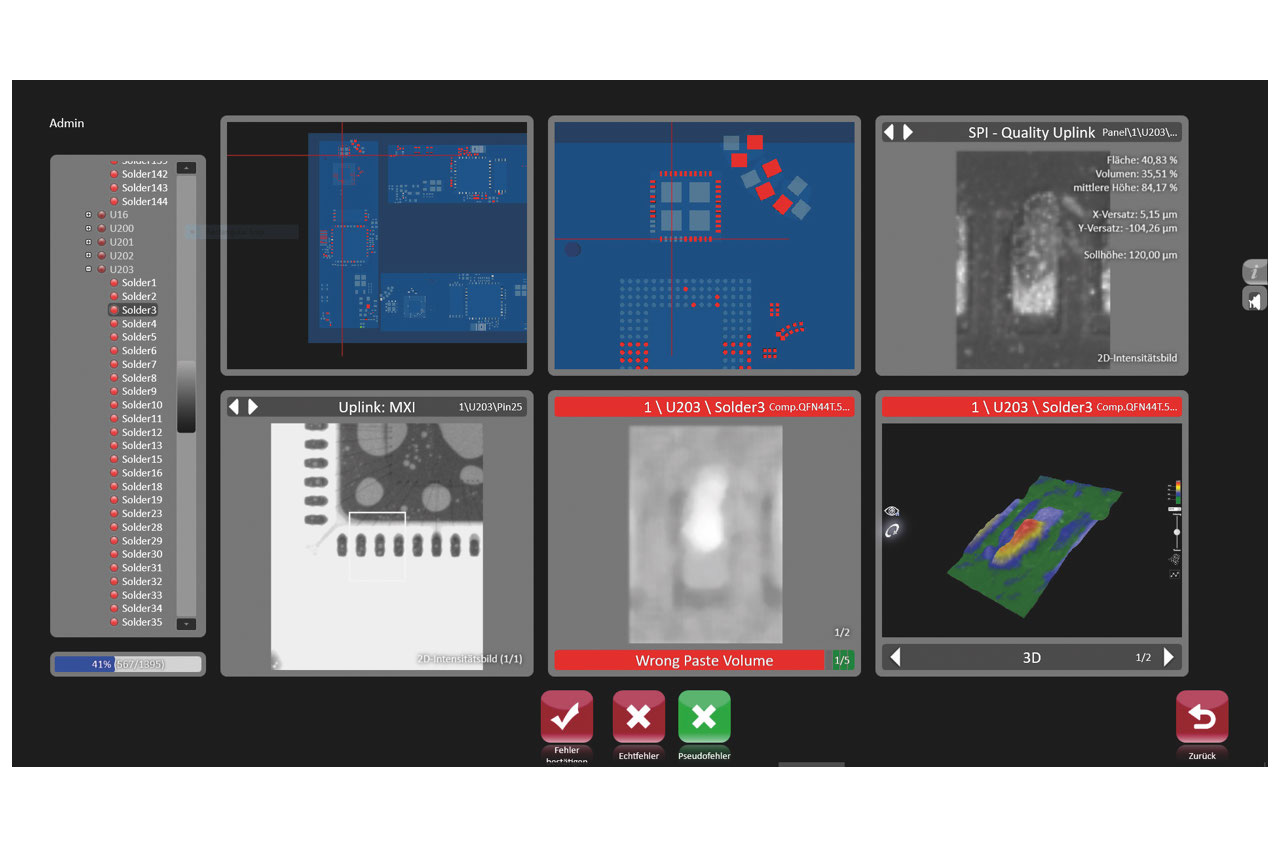
Working with the X8011-III is truly intuitive and easy to learn. For example, to inspect THTs or precisely identify voids in surface soldering, the analysis parameters can be selected and adjusted quickly and flexibly during operation. The system provides a clear overview of the tools required to create an inspection plan for automatic X-ray inspection. If, for example, shadowing of interfering components prevents an optimal image result, 3D reconstructions can be achieved with the aid of computed tomography for better localization of defects. The options available for this are part of Viscom’s XVR software. Individual layers of the irradiated object provide non-destructive information on whether or not a manufacturing defect is actually present.
The versatility of the X8011-III enables smart networking with Viscom inspection systems that are integrated into the production line. The overlap between MXI and AXI properties is therefore clearly evident in this context too. Inspection data from the solder paste inspection (3D-SPI) and post-reflow systems (3D-AOI and 3D-AXI) can be compared at a verification station with the highly detailed 3D-MXI results – for example, to determine the exact cause of recurring defects. The manual X-ray system reads the inspection plan from the production line to automatically approach only those positions on an assembly that actually need to be verified. As a new team player in the production process, the X8011-III X-ray system is set to deliver effective long-term results for cost optimization, improved process reliability and increased product quality.
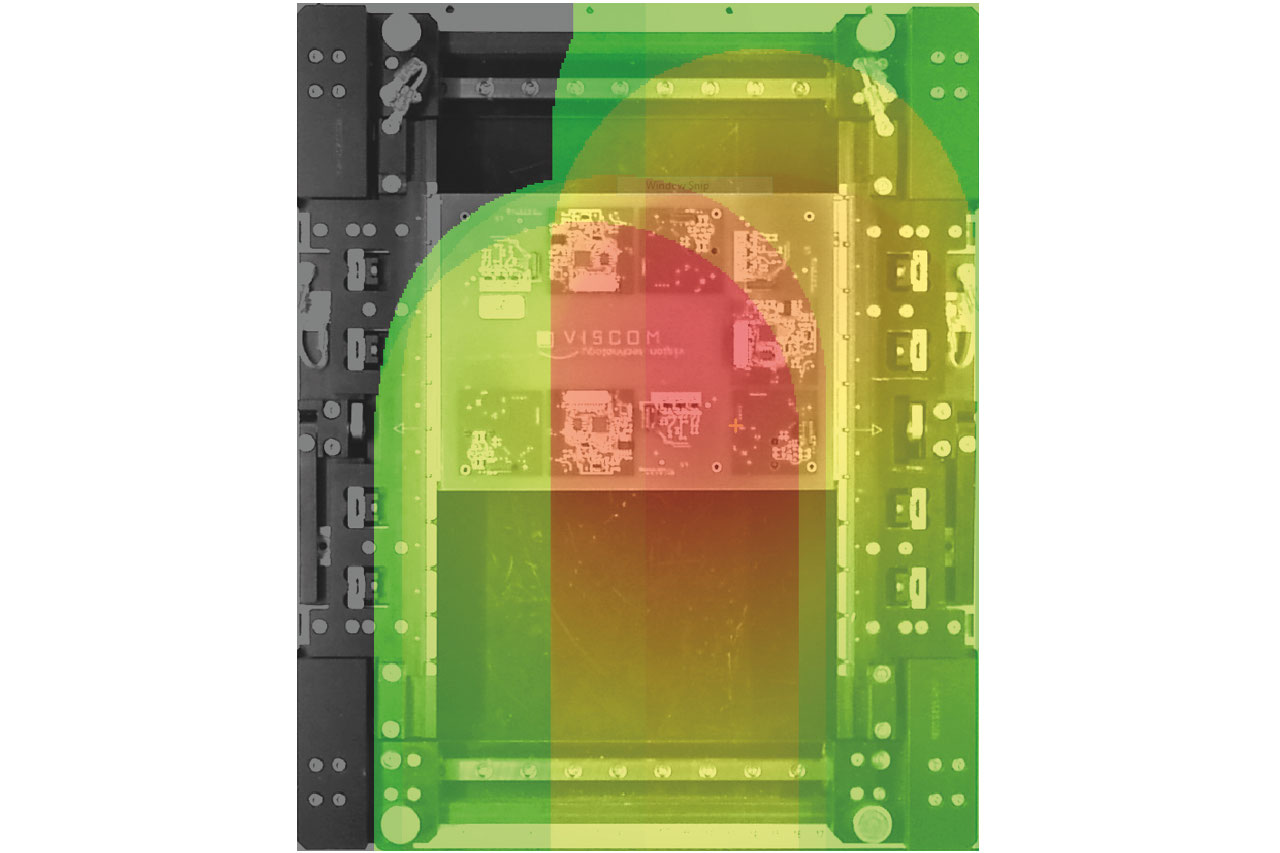
This also includes all-round informative documentation. Where in the past only X-ray images tended to be available, today professional reports with result and system data are generated automatically. A very practical component of such reports typically includes radiation dose information (heat map). Based on the X-ray examination, the system operator receives an overview of the corresponding values and also a visual representation including a color scale. On this basis, corresponding limit values and warning levels can be set during the X-ray inspection. This makes the X8011-III ideal for inspecting radiation-sensitive components in a way that is both specific and material-friendly.