Customers looking for leading-edge test solutions can come to Seica’s booth 2511 and view the newest line of Flying Probe test on the market in the form of the PILOT VX platform, bed of nails ICT solutions, the Compact LR, and Mini200 and the latest conformal coat inspection systems, the Dragonfly.
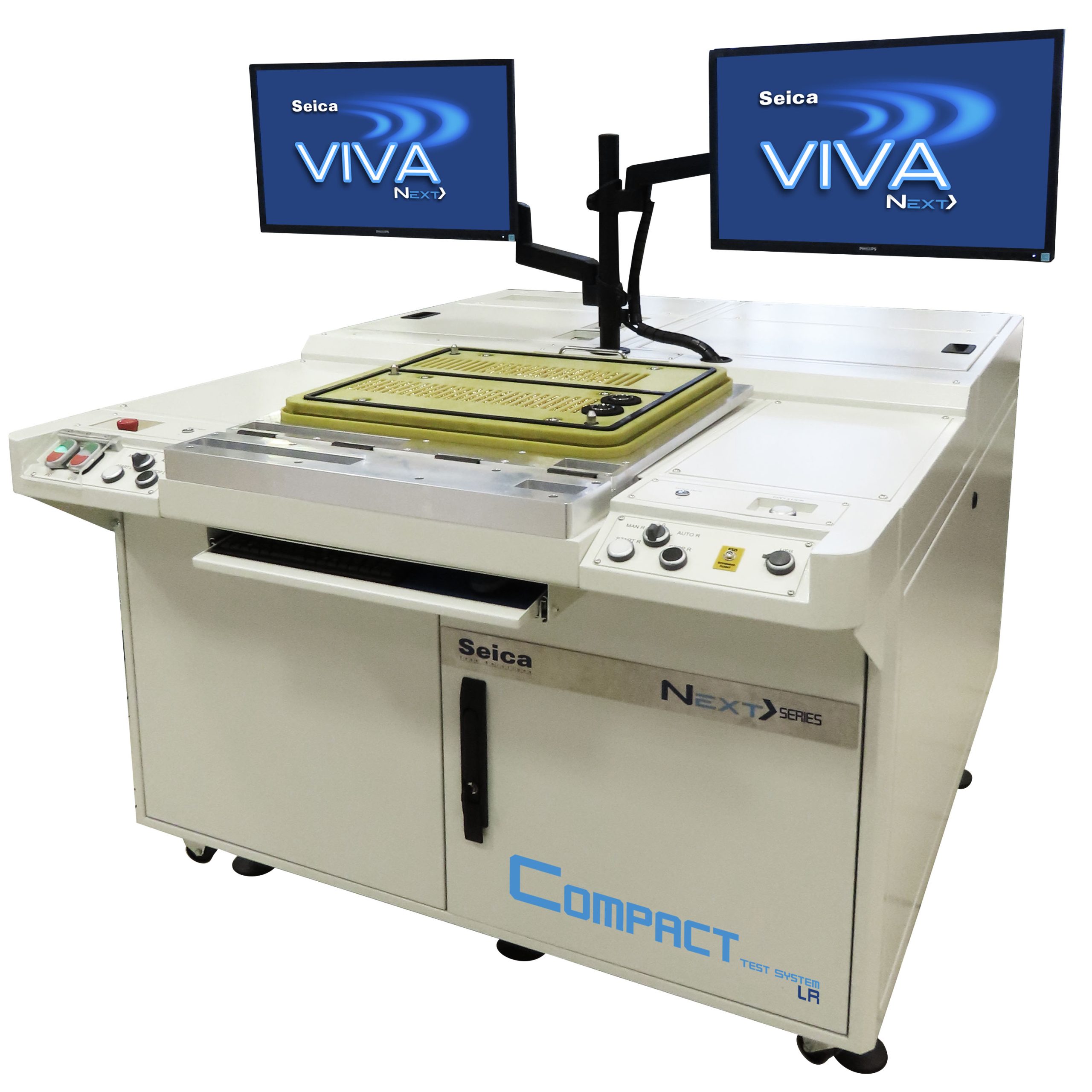
Visitors to Apex 2023 will see the premiere of the Compact LR, the latest addition to Seica’s already well-known in-circuit bed of nails and functional test solutions included in the COMPACT Next line. Seica’s COMPACT line of test systems are already the solution of choice for many contract manufacturers and OEMs, and the Compact LR provides additional legacy replacement capabilities for customers looking to replace test systems which are no longer supported by the original manufacturers. This new configuration joins Seica’s existing legacy replacement solutions for in-circuit testers such as Aeroflex/Marconi as well as for functional testers including Computer Automation, Schlumberger/Factron, GR179X, and GR275X series, and Teradyne’s L2XX, and L3XX. The Compact LR on display addresses the challenge of allowing redeployment of Teradyne Spectrum 8851 and 8852 fixtures onto a modern platform which includes all of the technologically advanced performances required by new applications, while at the same time allowing developers to continue to use their traditional standard fixture design.
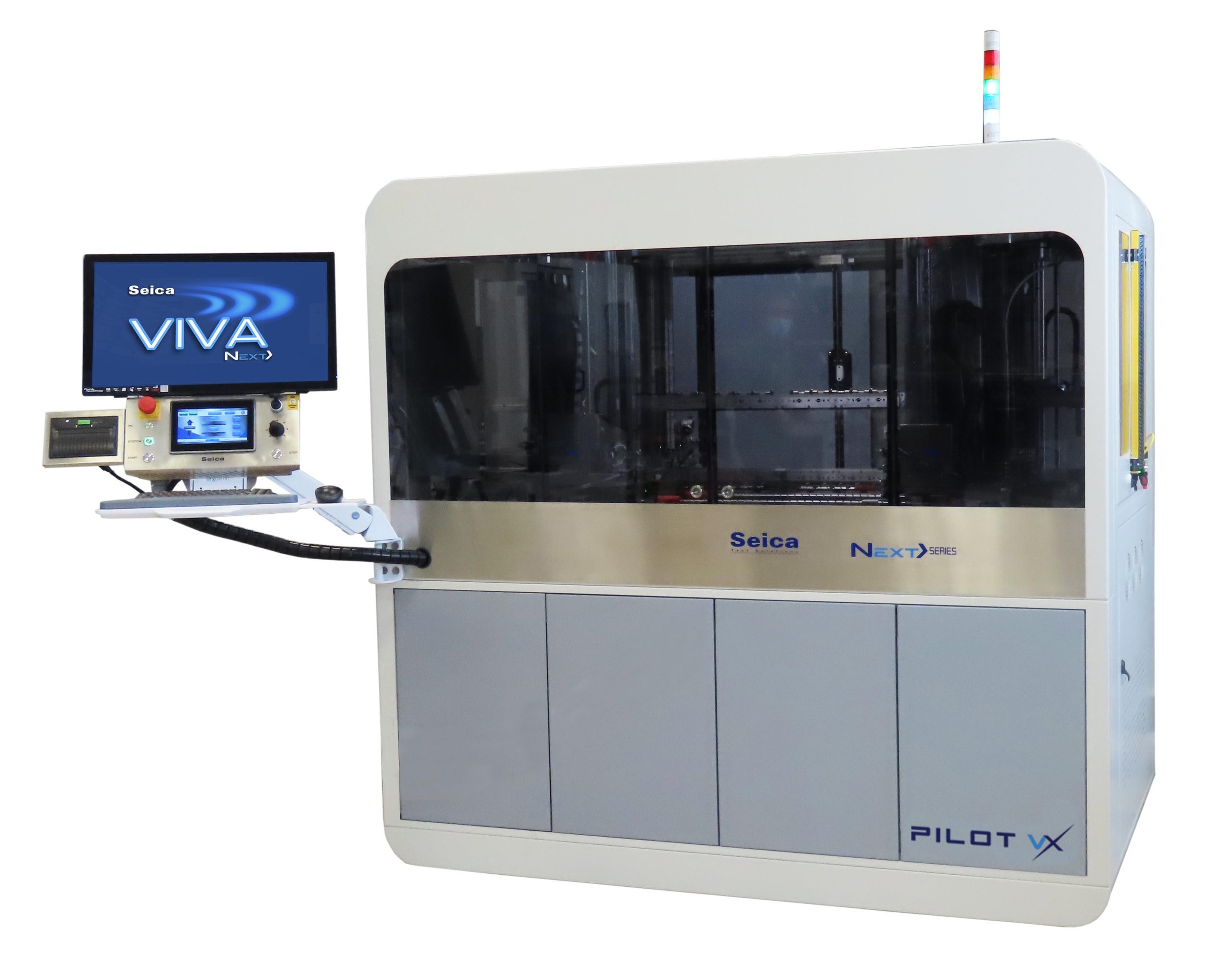
Seica will also be showing the Pilot VX, the gold standard for flying probe test performance, with new cutting-edge solutions that address the fundamental concerns of electronic board manufacturers looking to optimize their investment, from prototyping to production test. These new solutions, along with the dramatic improvements in speed and performance achieved in the Pilot VX platform, has now made flying probe test a key solution in many high-volume production environments with a high level of automation, but the Pilot VX platform also includes an extensive suite of measurement hardware and software tools to enable the test and validation of prototypes quickly and with minimum effort, a process that is generally the first thing that comes to mind when a flying prober is mentioned. Seica has added many advanced capabilities and tools that specifically address the needs of designers when testing prototypes. Having physical access to the circuit is a basic requirement for applying stimuli to a circuit and measuring the result. With the ability to probe even 35 µm pads the PILOT VX enables precise physical access to even very small targets, and the powerful Flylab software allows you to “interact” with your electronic board as if you had eight probes in your hand and a table of instruments available on your bench. The Pilot VX is ready to be used to perform validation, prototype or production testing, without requiring deep specific training on the tester or generating a test programs. Contact points can be selected manually using the integrated cameras and clicking on the graphical board image, then the simple and intuitive software interface enables the performance of parametric and functional measurements by simply selecting the type of measurement and entering the value. The system automatically positions the mobile probes and the measurement result appears on the integrated oscilloscope. Moreover, the PR boost feature provides the capability to power the board (up to 2A per probe) with all of the 8 standard electrical probes, to enable the test of active circuits and other functional tests which are an essential part of the design validation process. The Thermal Scan option is another useful validation tool, allowing the user to acquire a profile of the powered up board to check the thermal behavior of the various sections of the circuit. The Pilot VX can also be used to generate pressure/force topology maps of the device under test using our innovative FlyStrain™ option. Once a necessity for traditional fixture-based solutions, Seica has migrated these new tools to the flying prober where testing of ceramics, wafers or specifized avionics and satellite boards requires delicate probing and traceability.
SEICA’s VIVA software platform also includes a fast, streamlined process to automatically generate and debug a complete test program starting from the board CAD data, enabling the immediate test of the prototype board to detect any manufacturing errors. Functional tests can be created easily, on the fly, with the powerful QuickTest software, with only the knowledge of the circuit to be tested (and not necessarily the tester or programming language). The FlyPod option extends testing capability even more by specializing a single mobile probe to carry up to 14 channels, enabling access to boundary scan circuits and adding onboard programming capability without any external FIXED cables.
For designers tasked with the implementation of the original functional test spec, the MINI 200 included in Seica’s MINI Line, provides a wide range of integrated instruments, switching matrices and user power supplies, making it a very useful and cost-effective platform to develop your customized test benchmark. In addition, unlike most self-manufactured “rack and stack” test beds, Seica’s MINI test solution, with its standard “core” VIP™, complete user documentation and a self-diagnostic program, guarantees its sustainability and maintainability over time, even in the case of resource turnover. The user has broad discretion in the choice of configuration and programming languages: Seica’s VIVA Integrated Platform (VIP™) allows easy integration of off-the shelf instrumentation, and test sequences can be developed using the VIVA Test Studio environment as well as a wide range of third-party software including LabView©, TestStand©, C, and Python. Moreover, the programs developed on the MINI are completely transportable to other SEICA systems which makes for fast and easy setup of the manufacturing test process.
Visitors to Seica’s booth will also be able to view the Dragonfly, an automated optical inspection solution for conformal coat and through-hole-technology (THT). On display will be the desktop hybrid version, which has the new parallax LED scanning system with an innovative LED design, enabling it to switch from conformal coat inspection to THT inspection. With advanced optical technology, the Dragonfly can detect a multitude of defects such as contamination, delamination, air gaps, splashes, voids and peeling, to name a few. The benefits of the Dragonfly are ease of programming, lower costs of test, almost zero maintenance costs compared to traditional AOI systems, and dual hybrid test capability.
About Seica S.p.A.
Founded in 1986, Seica S.p.A. is an innovative, high technology company that develops and manufactures leading-edge solutions for the test, selective soldering of electronic boards and modules as well as a complete line of board handling and automation solutions. Seica also provides battery test solutions, automotive electronic board test solutions, infotainment test, as well as electric vehicle inverter and battery charging station test systems. Seica has fully embraced the concept of Industry 4.0, developing solutions to monitor and collect information from machines and industrial plants to enable the optimization of manufacturing processes, maintenance and energy management.
Company headquarters are located in Italy, with direct offices in USA, Germany, China, Mexico and France. www.seica.com.