The MES developer iTAC Software AG and SMC Deutschland GmbH, a specialist in pneumatic and electrical automation technology, are creating new monitoring and maintenance options in production. For this, the partners integrate sensor and actuator data into the MES solution using the iTAC.IIoT.Edge solution. In doing so, the SMC sensor data is transferred to the iTAC.IIoT.Edge via an IoT gateway. The stored data from the sensors and the MES is then analyzed and processed. They form the basis, for example, for automated detection and prediction of production problems in real time. iTAC will present the solution at productronica 2021 from November 16 to 19, 2021 in hall A3, at booth 161.
“In production, undetected leaks in the compressed air system can lead to increased or expensive air pressure consumption and, possibly, to unexpected production disruptions or downtime. For example, if a leak in the compressed air system causes an increased demand for compressed air, the compressor has to use more energy to ensure the supply of compressed air. In most cases, such a malfunction goes unnoticed and thus leads to increased costs. A monitoring instrument can detect increased compressed air consumption at an early stage. However, as the sensor data can show large variations during normal operation depending on the type of product, monitoring instruments with predefined threshold for determining the system status prove to be ineffective,” explains Peter Bollinger, CEO of iTAC Software AG.
Gaining insights from MES and automating processes
The Manufacturing Execution System iTAC.MES.Suite in conjunction with iTAC.IIoT.Edge is now able to correlate and interpret the measurement data with product and machine information. iTAC’s edge software solution combines streaming and batch analytics on a central scalable platform with out-of-the-box access to MES data. In doing so, the iTAC.IIoT.Edge uses data from the sensors in conjunction with the MES data to determine dynamic warning thresholds for various system parameters. The aim is to monitor these in real time.
This is possible with the solution developed by iTAC and SMC. Here, SMC transfers the compressed air sensor data via a gateway into an IoT platform and then combines it with the corresponding MES data to process the relevant data using modern algorithms.
These findings allow abnormal operating conditions to be detected and appropriate maintenance measures to be initiated. Early detection of increased air consumption thus identifies expensive energy peaks. “In general, it is important to avoid increased energy consumption, as this is very cost-intensive for manufacturing companies. With our new functionality, it is possible to quickly correct this energy consumption and thus return it to normal levels,” explains Peter Bollinger.
From the sensor into the MES – iTAC and SMC combine competencies
iTAC adds its many years of expertise to the solution in the area of controlling and optimizing production processes using MES. In addition, iTAC.IIoT.Edge provides an IIoT solution that allows MES and IIoT data to be linked using modern methods. SMC is incorporating its expertise in the shopfloor area with the sensors and actuators. The IoT platform used is both cloud and on-premises capable. Optionally, a hybrid approach can be selected, which further increases flexibility.
Peter Bollinger says: “As the new instrument is an integrated part of our iTAC.MES.Suite in combination with the iTAC.IIoT.Edge solution, users in production can continue to work in their familiar software environment without having to deal with the technical implementation of the new intelligent monitoring functionalities themselves.”
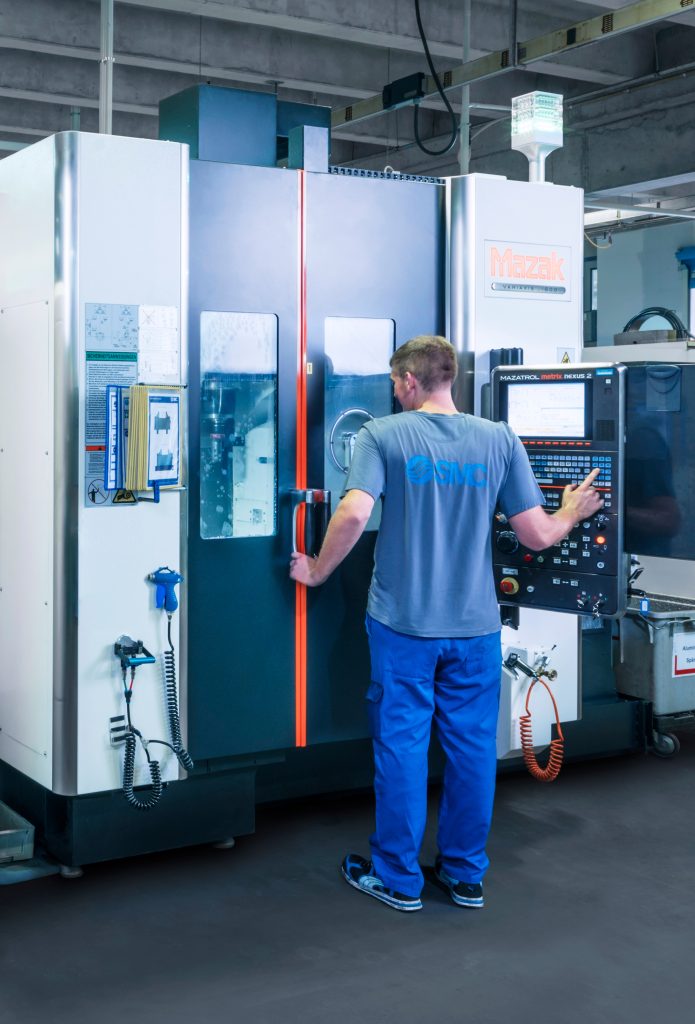