Since 1967, Hardmeier Electronics AG has been developing and producing innovative electronic devices and systems for measurement, control, and regulation technology. Within the Hardmeier Holding, comprising Hardmeier Electronics AG and Regatron AG, the company possesses high level of R&D and manufacturing expertise. This enables customer ideas to be quickly and efficiently transformed into new products. As part of its service offering, modern electronics manufacturing is included.
In surface mount technology (SMT) manufacturing, there has been numerous efforts to find solutions to improve material management and component storage. Primarily, the aim was to make the costly setup of orders, the storage and retrieval of components significantly more cost-effective. The constant pressure from customers and markets towards more flexible manufacturing, fluctuating batch sizes, frequent product changes, and higher demands on on-time delivery, emphasizes the importance of material management in manufacturing.
Hardmeier initiated an optimization project to improve their operation with a new system that was cost-effective for the size of its manufacturing operation. Essemtec was approached as a solution partner.
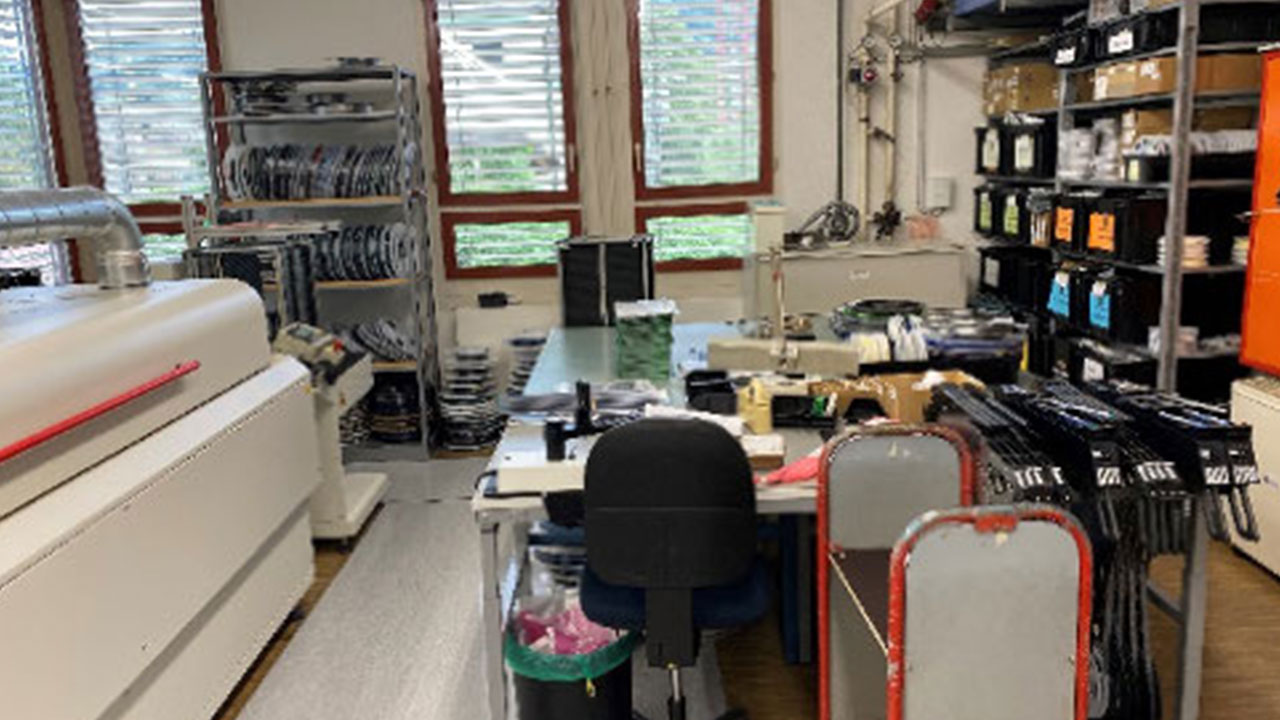
Under the motto “the right material, in the right quantity, at the right time, in the right place,” the project was defined. The following key needs were recorded as specifications:
Requirements
- The system must manage and intelligently store 3000-4000 SMD packages.
- The system must fit into the existing premises and be located as close as possible to the production line.
- The system must be able to track items from the reception of the goods through their storage and to the setup at the production line.
- d. Large range of storage type such as drying cabinets must be , and the integration with the existing ERP system is a must.
- Using one source of data for material handling
- The Return on Investment should not exceed 2 years.
- The system should be expandable in the future.
Solution Implemented at Hardmeier Electronics AG
Essemtec AG and its partner Arcadia generated the following solutions for the difference steps of material management:
- Components Reception & Identification
Using Arcadia’s incoming station, linked with the Essemtec Falcon Solution, the user could easily input and label incoming material. Upon reception of the packages, the manufacturer’s production information is read and compared with the Hardmeier item master in the database. The system only releases the items if the data identity is confirmed. The corresponding item receives a unique identification barcode, and the databases are automatically synchronized through Essemtec Falcon software suite.
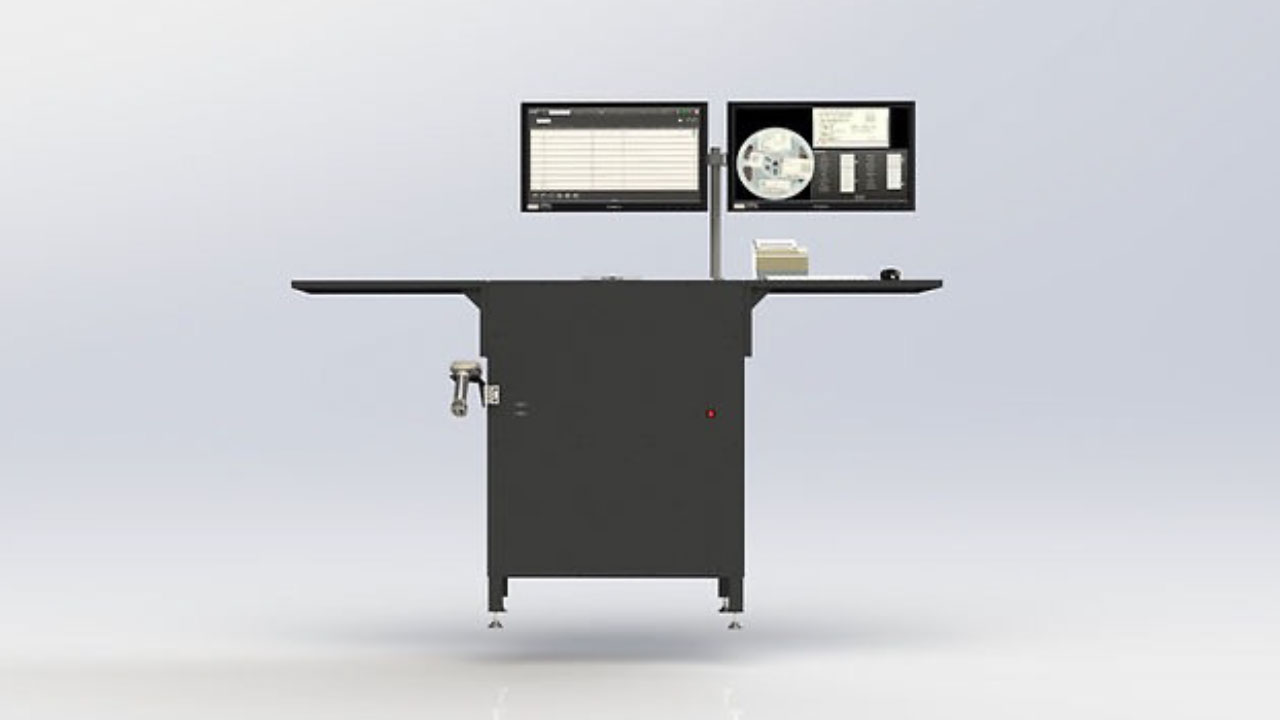
- Storage
The reels and packages are transported from the incoming station to the “pick by light” storage next to the production line and stored effortlessly after a barcode check. The operator is guided by LEDs. The storage positions are automatically recorded in the databases.
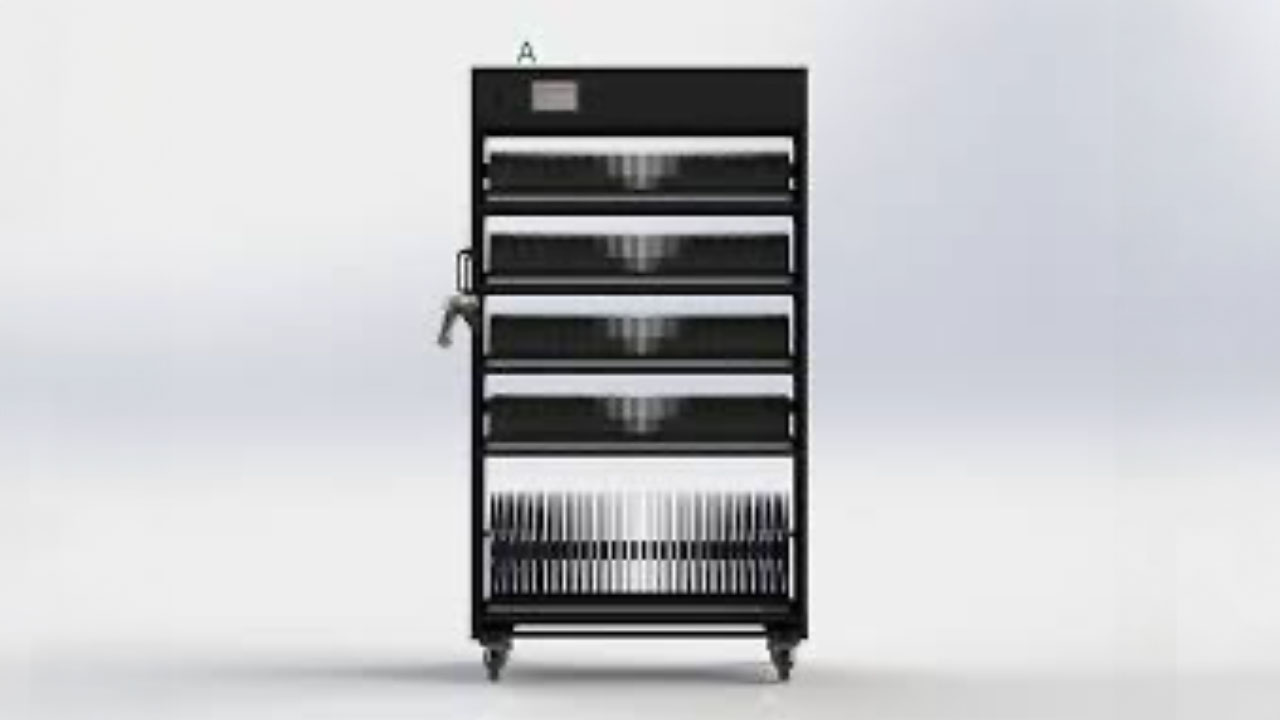
- Job Preparation
When the next production order is called up, Essemtec Falcon ensures that all the reels needed to be used light up, both in the warehouse and on the machines. Possible barcode storage positions are also displayed. The operator now collects the material without paper lists and starts setting up the required feeders with a significant time gain and a reduction of mishandling errors.
- Retrofitting in Production
Since all systems are interconnected through Essemtec Falcon, components to be retrofitted are called up from the machine in the storage unit in time. The operator receives a notification and only needs to pick up the reels that light up and start the retrofitting. The component quantities are automatically debited correctly in the databases with each pick. Operators, production and logistics supervisors could know exactly how many components of each type are available.
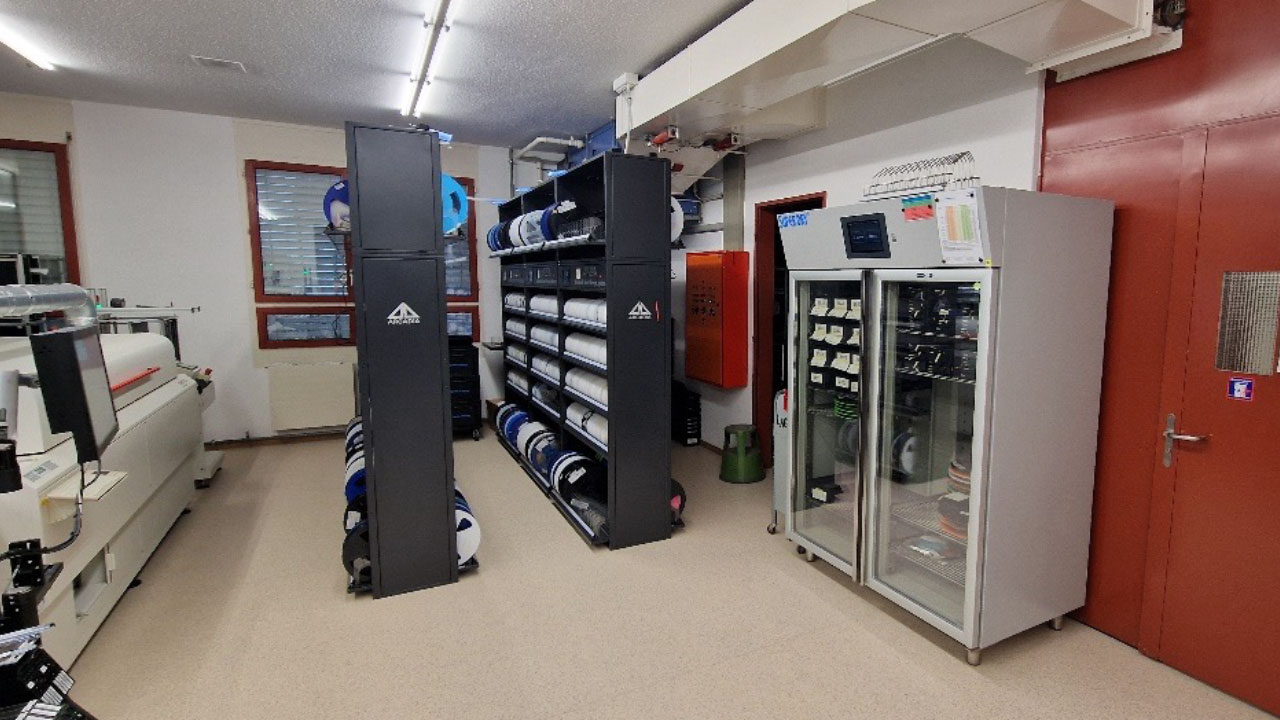
Benefits
Mr. Hary Kündig, Production and Purchasing Manager at Hardmeier Electronics AG, comments on the new system:
“A key aspect of the material management system is that SMD reels are tracked from reception to final consumption across all systems such as storage, production machines, etc. Every warehouse movement is tracked in real-time. The storage system, the machines, all databases, and the ERP system are now interconnected and synchronized thanks to Essemtec Falcon Software.”
“We are now about 5 times faster in setting up a new job and also during retrofitting in production. Our line downtimes have significantly decreased, and the operators work more relaxed. The tedious and time-consuming search for reels no longer exists, and the Return on Investment will be in the expected range. Our high expectations for the system and Essemtec Solution have been more than fulfilled.”
Meet Essemtec at SMT Connect – Hall 4 Booth 2009.
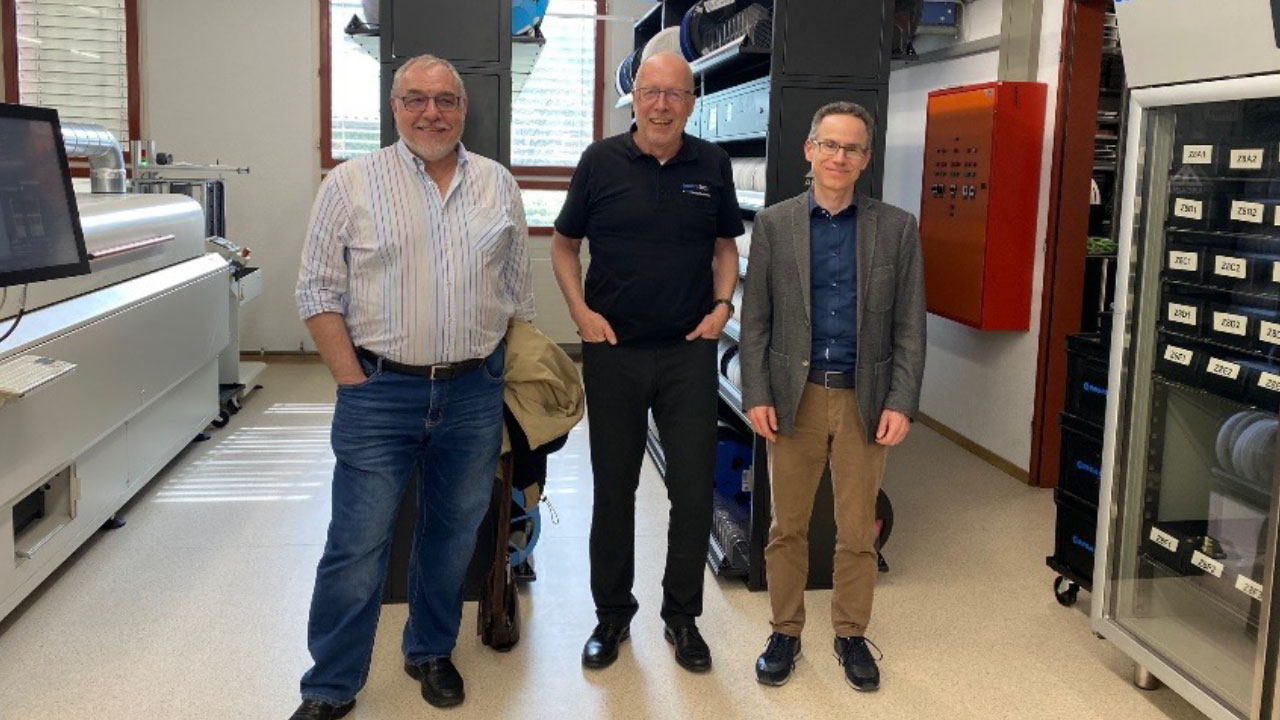